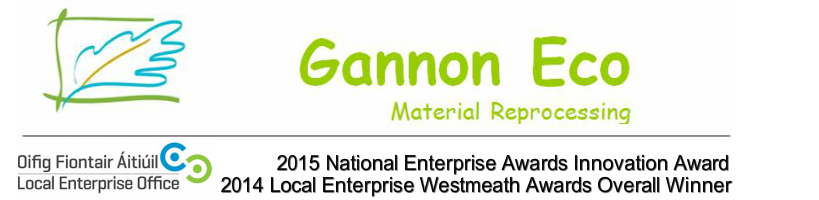
Name : John Gannon Concrete Ltd, T/a Gannon Eco, C/o Niall Gannon
Address : Hazelwood, Kilbeggan
Project : Sustainable solution providers for industrial waste streams.
Website : www.gannoneco.ie/
How did Gannon Eco start up?
John Gannon Concrete Ltd is a precast concrete manufacturing company incorporated in August 2007. John Gannon Concrete is a producer of concrete moulding products, mainly precast walling systems and sign bases for the recycling, agriculture and construction sectors. The waste material processing business, Gannon Eco has been trading under this company.
What does Gannon Eco do?
Gannon Eco has expanded its service since its inception when it established itself as a glass reprocessing service. Gannon Eco are solution providers for industrial waste streams. Gannon Eco reuse or remanufacture 100% of the material they receive at their site, they offer other recycling services to companies which including glass reprocessing, foundry casts and moulds, construction and demolition wastes, waste sands and clays, abrasives and abrasives compounds, gypsum powder and sludges, ceramic and plastic sludge reprocessing and reuse. Waste stream items are reprocessed at Gannon Eco and recycled as raw material for products directly marketed and sold by Gannon Eco.
What is the end product from Gannon Eco?
Their main products being crushed glass media for waste water filtration, crushed glass media for industrial abrasives, raw materials for foundry moulds, road marking and fiberglass. Gannon Eco also supplies raw material ceramic sludge as a fill material for their own range of Eco Concrete Products.
Quote Niall Gannon after he completed the LEAN Pilot programme from LEO Westmeath:
‘ The objectives of the assignment was to introduce Lean into our growing enterprise. What we did was have the processes mapped from collection through production and dispatch to customers. We also changed process to eliminate double handling of product in the production process.
We identified two main issues
- One was machine downtime and we started a preventative maintenance programme to reduce the downtime.
- The second was less production during shift change. We overlapped the starting and finishing of shifts by 30 minutes. Lean resulted in us being able to eliminate double handling, reduced downtime and resulted in a 15% increase in output’.